Concebido en la década de 1950 en las fábricas japonesas de Toyota, el modelo Lean se ha impuesto como un enfoque fluido y favorable para la gestión de la producción destinado a reducir los desperdicios y garantizar una mejora continua.
Orientado inicialmente al sector industrial, el modelo Lean se adapta perfectamente a muchos ámbitos —hablamos por ejemplo de gestión Lean, start-up Lean o incluso de informática Lean, según el campo de aplicación— y los marcos de trabajo más recientes, como Scrum (derivado de Agile, otro movimiento surgido en paralelo al Lean), ahora se vinculan directa y explícitamente con este modelo. Esta apertura a nuevos horizontes permite concebir nuevos usos para las múltiples herramientas y prácticas del Lean, como Kanban, Mudas, Kaizen o el método 5S. Es en esto último (el método 5S) en lo que nos centraremos en este artículo, especialmente en cómo recurrí a este concepto para gestionar un product backlog en un contexto Scrum, pero volvamos primero al origen de su uso en la industria.
El método 5S como herramienta Lean y en la industria
El método 5S es una herramienta Lean utilizada principalmente en el entorno industrial, y más concretamente en la organización de tiendas y talleres. El 5S permitirá, por ejemplo, organizar los materiales (tornillos, sensores, motores, etc.) de forma clara para todos.
El modelo Lean describe el 5S como un método de mejora que tiene por objeto principalmente reducir el desperdicio, especialmente en términos de pérdida de tiempo, simplificando todo lo posible y eliminando lo innecesario.
Las 5 operaciones del método 5S
Al igual que muchas herramientas Lean, los términos están en japonés. El 5S consta de 5 pasos que deben realizarse uno tras otro en el siguiente orden:
- Seiri (organización): Suprimir lo innecesario
- Seiton (orden): Situar las cosas
- Seiso (limpieza): Sanear
- Seiketsu (normalización): definir normas a Seguir
- Shitsuke (educación): Seguir y progresar
- Seiri : el primer paso es identificar y eliminar lo innecesario. Cualquier cosa que no se use normalmente debe reciclarse, desecharse o archivarse. Identificaremos lo que debe colocarse más cerca del lugar de trabajo porque es lo que debemos usar primero o con mayor asiduidad. El objetivo es aumentar la concentración eliminando distracciones e interrupciones.
- Seiton : el propósito de este segundo paso es evitar perder tiempo y energía clasificando los elementos de la manera más lógica posible. Seiton a menudo se parafrasea como «Un lugar para cada cosa y cada cosa en su lugar». Por tanto, agruparemos elementos similares categorizándolos. El resultado de este paso es un entorno de trabajo donde la búsqueda de un elemento específico se ve facilitada por su organización. Favoreceremos, sin ser obligatorio, la gestión FIFO (First In First Out, o «Lo que llega primero sale primero», como en una cola de espera, por ejemplo), y no LIFO (Last In First Out, o en «Lo que llega último sale primero», como en una pila de platos).
- Seiso : para este tercer paso se buscará evitar, en la medida de lo posible, la aparición de futuras anomalías facilitando al máximo su detección. De este modo, limpiaremos nuestro entorno de trabajo y repondremos/repararemos lo que sea necesario. Se trata del primer paso hacia la autogestión y el mantenimiento sistematizado del entorno laboral y sus elementos.
- Seiketsu : este cuarto paso es el de la estandarización: se trata de definir las reglas que permitirán evitar en lo posible que el desorden llegue a instalarse. Es recomendable utilizar lo máximo posible la gestión visual y el etiquetado. Por ejemplo, en un taller, pintaremos con aerosol la mesa de trabajo para que la forma de cada herramienta quede presente, de modo que podamos notar fácilmente dónde guardar una herramienta y/o si falta una.
- Shitsuke : el objetivo de este quinto y último paso es educar a todas las personas implicadas en el entorno laboral para que la práctica de las 5S se convierta en un hábito diario. Para que el método 5S no sea un fracaso (véase más abajo), es necesario que todos se adhieran a las reglas de estandarización y organización que habremos puesto en marcha. Por ello, es recomendable no imponer estas reglas, sino definirlas con los implicados con el objetivo de mantenerlas en el tiempo el mayor tiempo posible para no tener que volver a hacer un nuevo método 5S.
Equivalente en español: ORDEN
El 5S también podría utilizarse en español con el acrónimo ORDEN:
- Ordenar
- Reorganizar
- Desempolvar / Descubrir anomalías
- Evidenciar
- Nutrir el hábito
El método 5S aplicado a la vida cotidiana
¿Y si le dijera que lo más probable es que esté aplicando el método 5S de forma natural y diaria en casa sin siquiera darse cuenta?
¿No lo ve?
¿Si le pregunto cómo organiza su comida o su vajilla? Por ejemplo, los tenedores seguramente tienen un lugar específico en su casa, al igual que los platos, vasos, cuchillos, etc. Efectivamente, ha identificado espacios de almacenamiento específicos para cada uno de estos elementos, y si lamentablemente encuentra una cuchara donde están los tenedores, lo considera un error y lo soluciona con bastante rapidez. Del mismo modo, no se le ocurriría poner un tenedor sucio entre los limpios.
Piénselo la próxima vez que guarde los platos, observe todo lo que hace e intente asociarlo con cada uno de los pasos del método 5S.
Gestión de un product backlog con el método 5S
El método 5S se puede aplicar a la gestión de un backlog o a su reorganización cuando ha escaseado la gestión. Yo, personalmente, introduje el 5S en mi ámbito profesional para lograr este objetivo. La última vez que lo usé fue en un backlog compuesto por más de cien artículos, no todos definidos con la misma nomenclatura, con descripción o no y que contenían tareas obsoletas o importantes… La operación movilizó a buena parte del equipo y duró un día entero.
Antes de realizar este tipo de operación, por supuesto, le aconsejo que insista en el hecho de que no es nada deseable empezar el método 5S desde cero con regularidad y que es necesario ser disciplinado para mantener el sistema en perfectas condiciones de funcionamiento. Por ello, es importante hacer comprender a las personas implicadas que este proceso es costoso y doloroso, pero se torna irremediablemente necesario cuando se ha permitido que el desorden se imponga.
En resumen, he aquí la estrategia utilizada, en coherencia con el 5S, para ordenar de forma eficaz un backlog:
- Seiri: eliminar lo innecesario. Por ejemplo, aunque pueda parezca brutal, podemos definir una fecha a partir de la cual consideramos que los elementos del backlog han quedado obsoletos y archivar todos los elementos anteriores a esta fecha (por ejemplo, más de un año): los elementos que son realmente necesarios volverán a surgir sobre la marcha y así será posible evaluar más fácilmente la relación coste/beneficio de su consideración. Para ser menos drástico, también puede analizar cada elemento uno por uno teniendo a su disposición un representante del cliente o de los usuarios, o en su defecto, un miembro del equipo que conozca perfectamente el negocio, pero esto puede convertirse rápidamente en una tarea que consuma mucho tiempo, por lo que recomiendo combinar estos dos enfoques.
- Seiton: situar las cosas. Una vez completado el primer paso, se volverá a revisar cada elemento para, en caso de ser necesario, situarlo en el backlog correcto (en el caso de que el backlog inicial se refiera a varios productos) y priorizar las tareas entre ellos. Si no existe la posibilidad de definir fácil y rápidamente un valor de negocio y/o puntos de esfuerzo, es recomendable situar primero los elementos sobre los que se tiene mayor conocimiento y al revés, los elementos más vagos, al final.
- Seiso: hacer que todo brille como el Sol. Posteriormente viene la fase de limpieza: el objetivo será, sobre todo, facilitar la detección de anomalías y corregirlas si están presentes. Personalmente, aprovecho este paso para agregar los pocos elementos descriptivos que pueden faltar y reescribir el elemento en forma de historia de usuario si es necesario.
- Seiketsu: definir normas a seguir. Esto se puede hacer, por ejemplo (por un propietario de producto, que es el único responsable del backlog) mediante etiquetas y filtros, agregando reglas de adición (adición predeterminada en la parte superior o inferior del backlog), reglas de priorización de los elementos, un espacio intermedio para cualquier artículo que no esté listo (tenga cuidado, sin embargo, de que este no se convierta en un segundo backlog, por lo que será necesario asegurarse de que la vida útil de cada elemento sea lo más corta posible en este espacio intermedio), una «definición de preparado» o cualquier otro ajuste que se considere necesario. Atención: la estandarización debe seguir siendo sencilla para que su adhesión también sea lo más fácil posible.
- Shitsuke: educar. Para el último paso, el más importante en mi opinión, es necesario explicar cómo funciona el backlog a cualquiera que necesite visualizarlo (miembros del equipo, pero también gerentes y responsables de la toma de decisiones, por ejemplo). Lo mejor es partir de la observación del fallo y estructurar reglas de estandarización con las personas implicadas para finalmente llegar a una propuesta operativa concreta (basada, por ejemplo, en la gestión visual, que permite hacer comprensibles las reglas de gestión de un vistazo o incluso automatizarlas para que ni siquiera haya que pensar en ello). Esta propuesta no es definitiva, por supuesto que debemos fomentar la mejora continua, pero tenemos que estar atentos a la aplicación estricta del método 5S y, por tanto, de las reglas que se han decidido en conjunto, incluso si ello significa cambiarlas a medida que se reciban comentarios al respecto con el fin de evitar cualquier deriva que conduzca al fracaso del uso del 5S.
¿Por qué el 5S no funciona?
A menudo sucede que la aplicación del método 5S solo dura un tiempo y que encontramos nuestro viejo desorden, y como el caos atrae más caos, solo se necesita una pequeña excepción a la regla para que el trabajo del 5S se esfume de un plumazo. Es el caso de la pequeña historia de usuario que no se sitúa correctamente en el backlog, porque lo haremos «después»… y que lamentablemente nunca se organizará porque, como establece la ley de Leblanc, «después es igual a nunca».
Esto sucede con mayor frecuencia porque no se implantó el método 5S por completo. Tras la estandarización del cuarto paso (Seiketsu), muchos se quedarán ahí pensando que por fin tienen un backlog o un taller ordenado, práctico en el uso, ignorando el paso que, en mi opinión, es el más importante: Shitsuke, para educar en las prácticas. Al descuidar este paso, por restricciones presupuestarias o porque no lo consideramos necesario, favorecemos el regreso inexorable del desorden (una historia de usuario no almacenada en el backlog, luego una segunda, ya que, al fin y al cabo, hubo una primera, etc.). Elementos que se deben tener en cuenta sobre el backlog (para hacer la analogía con los marcos Agile): El modelo Scrum requiere disponer de un propietario de producto, lo que facilita mucho la última etapa del 5S, la más difícil, ya que este es el único que actúa sobre el backlog y, por tanto, es el garante de la aplicación del método. Recordemos, sin embargo, que Scrum exige que la comunicación del contenido del product backlog sea lo suficientemente clara para todas las partes interesadas (equipo Scrum, pero también partes interesadas), por lo que será relevante que, aunque el propietario de producto sea el único responsable para la gestión del product backlog, la estandarización de este es también se deriva de una reflexión que favorece la inteligencia colectiva.
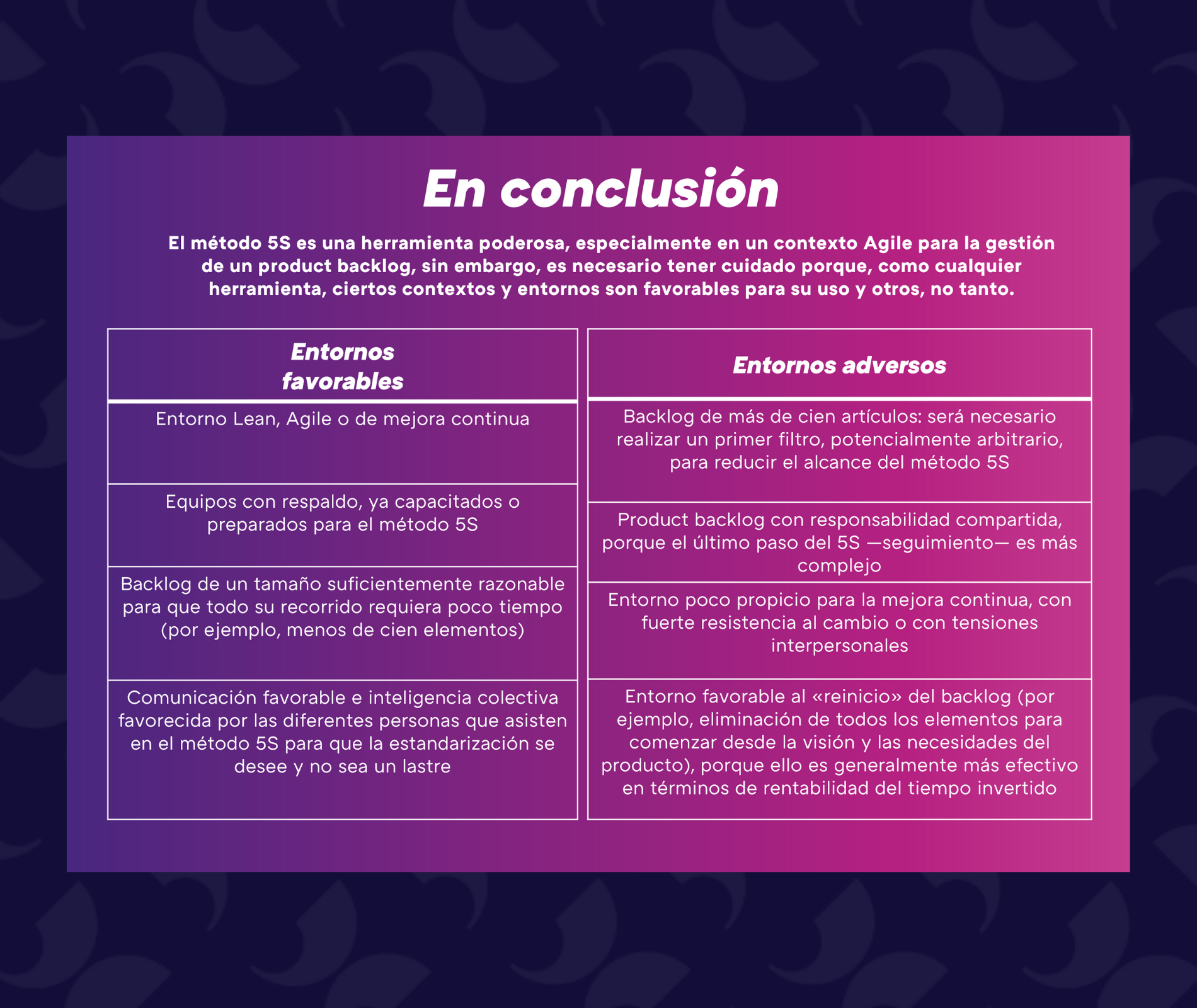